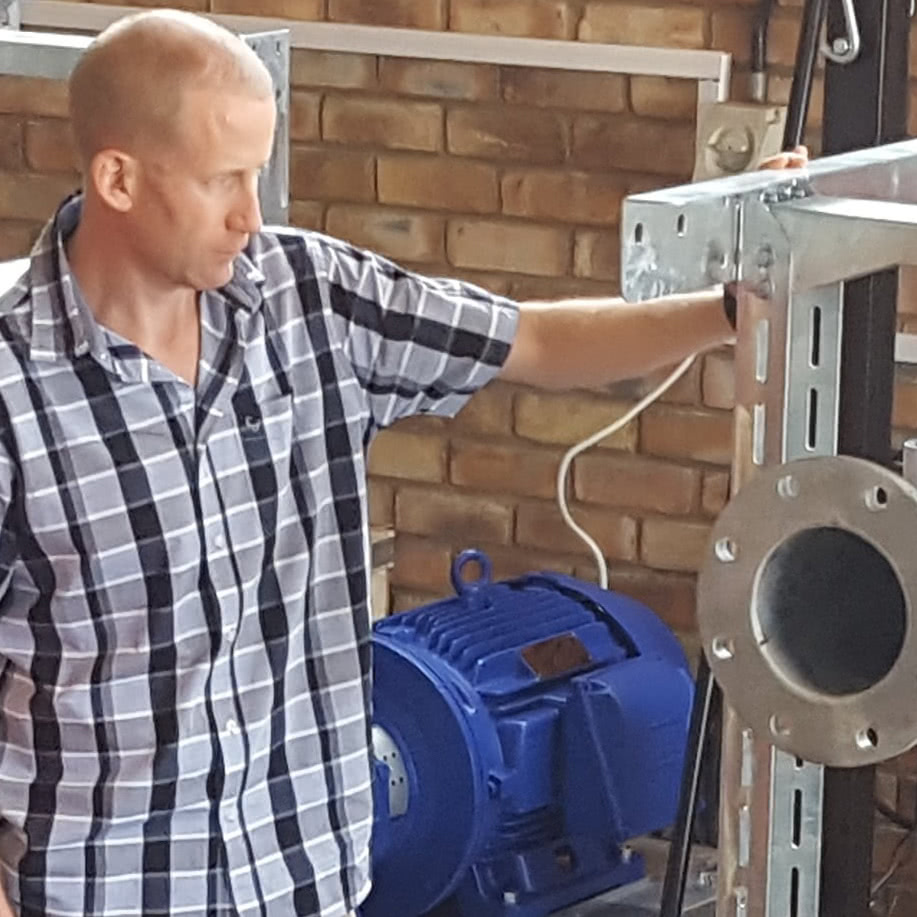
Murray Bredin
Chief Executive
Murray Bredin, Chief Executive of Shock Wave Engineering comes from a long line of KwaZulu-Natal dairy farmers and is well versed in the on-going challenge farmers face with rising production costs and lower farm gate product prices.
“It was while I was working on a specialised pump system for a client that I saw the opportunity to improve the efficiency of pump systems in agriculture, mining and industry.”
However, Murray chose to be an engineer completing a BSc Engineering (Aeronautical) degree at Wits in 1998 and his PhD in 2002 for a thesis titled The Measurement of Drag in Unsteady Compressible Flow.
He working career began in the nuclear field at Pebble Bed Modular Reactor and moved into the testing and measurement field assisting companies that needed to produce mechanical equipment as managing director for International Slurry Pump Solutions.
“It was while I was working on a specialised pump system for a client that I saw the opportunity to improve the efficiency of pump systems in agriculture, mining and industry.”
This led to the founding of Shock Wave Engineering in 2008 and the development of a sophisticated and unique system of measuring, controlling
and monitoring of pressure and flow rates using the optimal amount of energy to reduce energy use and provide savings, improve efficiency and better use of time.
Murray combined the tools he developed for his PhD Thesis and his knowledge of farming in developing an automated centre pivot pump control that provided an even flow of water for crops with a wireless monitoring system that enables the farmer to see what is happening on his fields from a website or a cellphone.
“My dad is a dairy farmer in Southern Natal with a relatively small herd. His focus has been on improving efficiency on his farm in every aspect, from pasture to feed and energy, rather than expanding his farm and herd like many other farmers.
“Like most people he believed that the electricity bill was just another bill that had to be paid and there was nothing that could be done to reduce it.”
So it was to the home farm that Murray went first to test his prototype.
“We found that there were huge energy losses with the irrigation system. They were so big that it made the capital investment worthwhile. Once fully functioning, the farm achieved energy savings of up to 75%. It also saved time and helped to use the farm labour more effectively.
“From here on it was a process of turning the prototype into a commercial product that was easy to implement. We developed our own electronics which brought down the costs of installation and website software interfaces.”
“While there may be other systems that save energy in a similar way this is the only one I know of that is flexible and does everything needed to save energy and monitor the pumps remotely in this environment.”
While saving costs on power should be music to the ear, Murray has been faced with scepticism and disbelief.
“It has been a difficult sell. When we say that a 40% saving can be achieved people are skeptical and we spend a lot of time on explaining the science. But, once people install a system and see how it works they come back for more.”