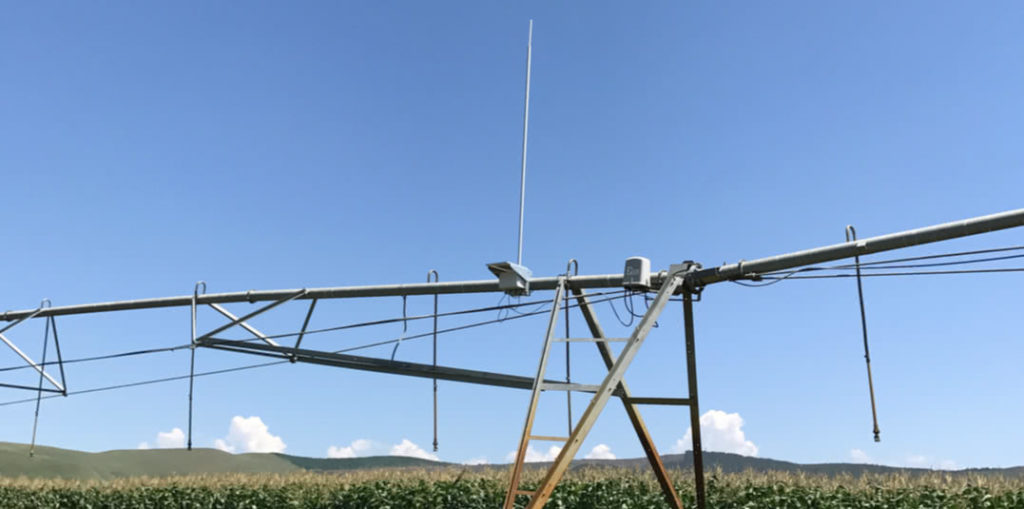
WE GUARANTEE A 15% ENERGY SAVING OR YOUR MONEY BACK.
- We undertake a Discovery Engagement Contract, where a full assessment of your pivot system is carried out to enable a comprehensive project scoping quote to be created.
- We use the data from the Discovery Engagement Report to provide you with a detailed quote. If you go ahead with the project you receive 50% of your Discovery Engagement contract cost back!
- Once installed, we initially run the equipment in test mode to verify the savings you can achieve.
- Should your overall savings not be at least 15%, then we reimburse you for the installation and remove the equipment.
Shock Wave Engineering will test the pump itself and the system as a whole.
Pump testing is performed to determine the efficiency at which the pump and motor converts electrical power into hydraulic power. The electrical power absorbed by the motor is measured using a power analyser. The hydraulic power is measured by measuring the flow rate and the increase in pressure across the pump. An ultrasonic transit time flow meter is used to measure the flow rate. This eliminates the need to cut into the pipe.
The system is tested as a whole to determine how efficiently the hydraulic power generated by the pump is utilised within the system. In many cases the flow rate or pressure generated by the pump is too high for the requirements of the system. Pressure is then dissipated through valves or flow is re-circulated. This is the equivalent of driving with the hand brake on.
Once actual operating data is gathered from the field it is post processed and a number of recommendations are made to the client.
Typically 4 or 5 options are presented, ranging from very inexpensive simple solutions (such as trimming an impeller) with moderate energy saving
potential to more expensive and complex solutions (such as a variable speed drive) with a higher energy saving potential. A cost benefit analysis can then be performed to determine the best option.
HOW MANY SYSTEMS HAVE BEEN INSTALLED?
Shock Wave Engineering has installed over 40 systems from the Western Cape to KwaZulu-Natal and Gauteng. Most of these systems are for centre pivot control.
WHAT IF SOMETHING GOES WRONG?
A major consideration in the design of this system is the fact that it is installed in very remote areas. Therefore the system has a built in fail-safe mechanism.
- If there is loss of signal from the remote pressure sensors the system ramps up to full power.
- If there is loss of communication with the web server the system continues to control with the current settings.
- If the control system fails the Variable Speed Drive (VSD) can be manually switched to full speed.
- If the VSD fails then a change over switch to the original star-delta starter can be used to operate the pump.
WHAT POWER SAVING CAN I EXPECT?
Energy saving depends on the losses in the system. Our experience shows that on average energy savings range from 20% to 50% although there are examples of a 70% saving.
We believe a minimum of 15% power saving can be expected and this we guarantee.
When the savings on each of various pumping system aspects are multiplied together the savings add up. For example a 10% saving on efficiency and 10% improvement on pressure amounts to a 21% saving.
WHAT OTHER BENEFITS ARE THERE?
Correctly automating your pumping systems ensures you make the most of Eskom’s Ruraflex Tariff and reduces your power bill. Automation makes full use of off-peak periods and ensures shut-down during peak expensive power usage periods.
Wireless data transmission eliminates the need to install long lengths of new cables across extensive farm fields.
WHAT WILL THE SYSTEM COST ME?
Typically Shock Wave Engineering will present the client with 2 or 3 options, ranging from very inexpensive simple solutions with moderate energy saving potential to more expensive and complex solutions with a higher energy saving potential. A cost benefit analysis can then be performed to determine the best option.